Zhengzhou ChangHeYue New Material CO.,LTd
Medium temperature graphitized petroleum coke
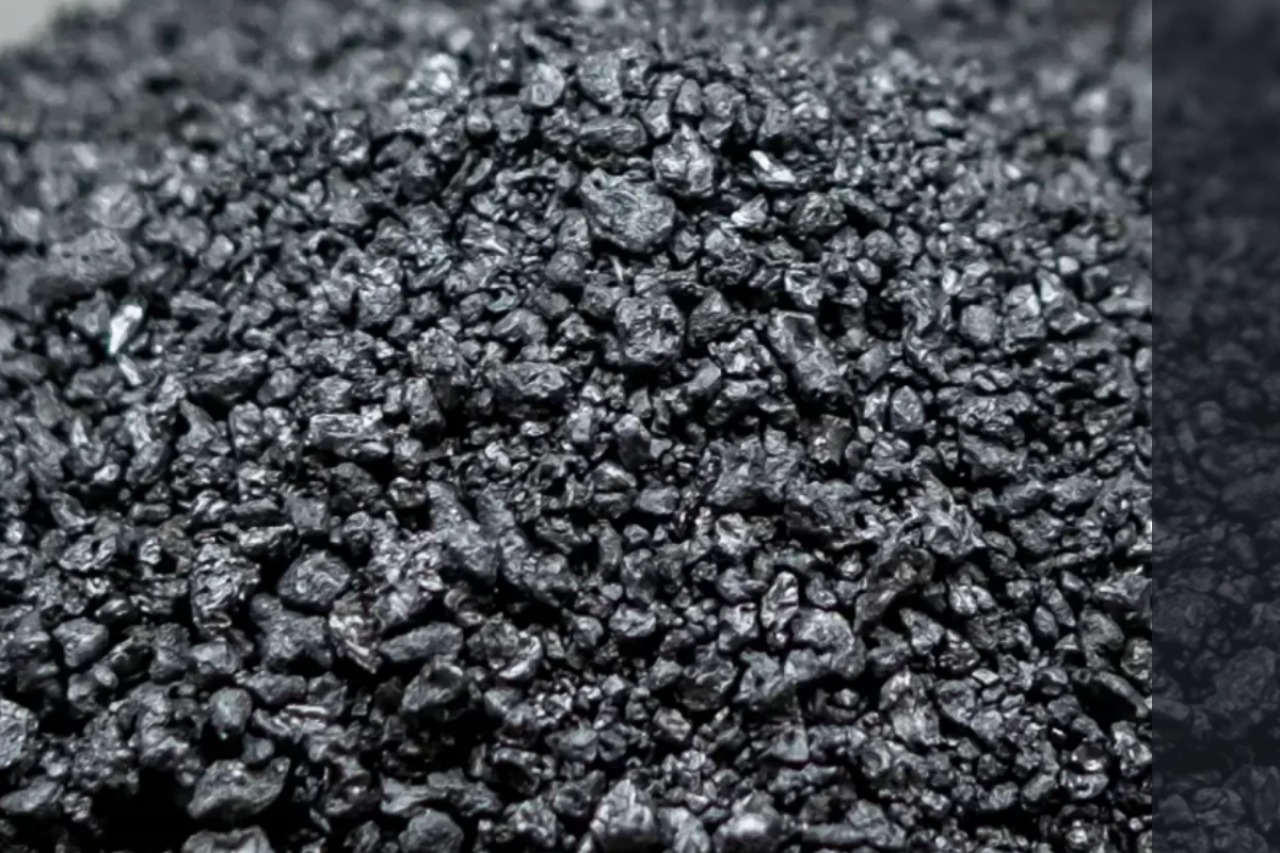
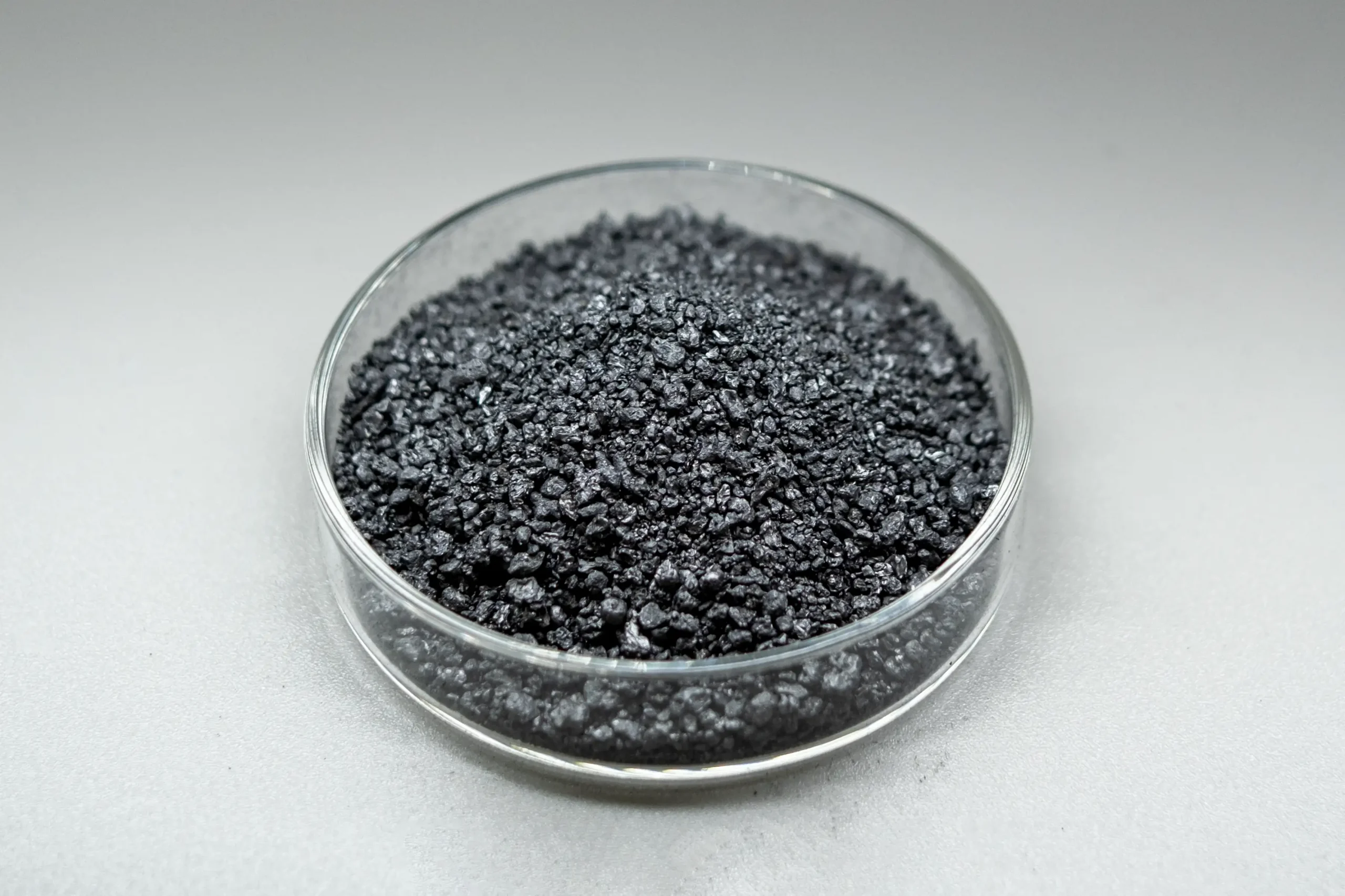
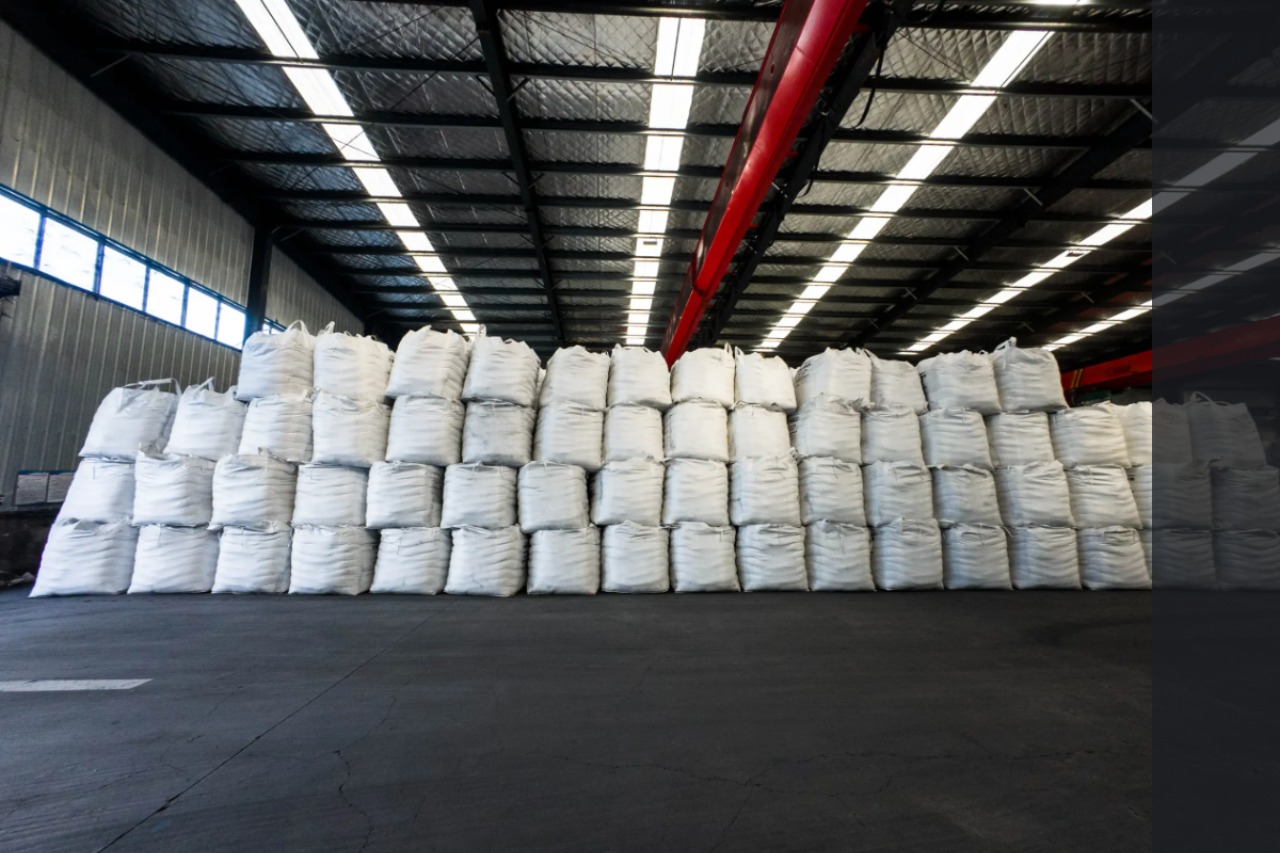
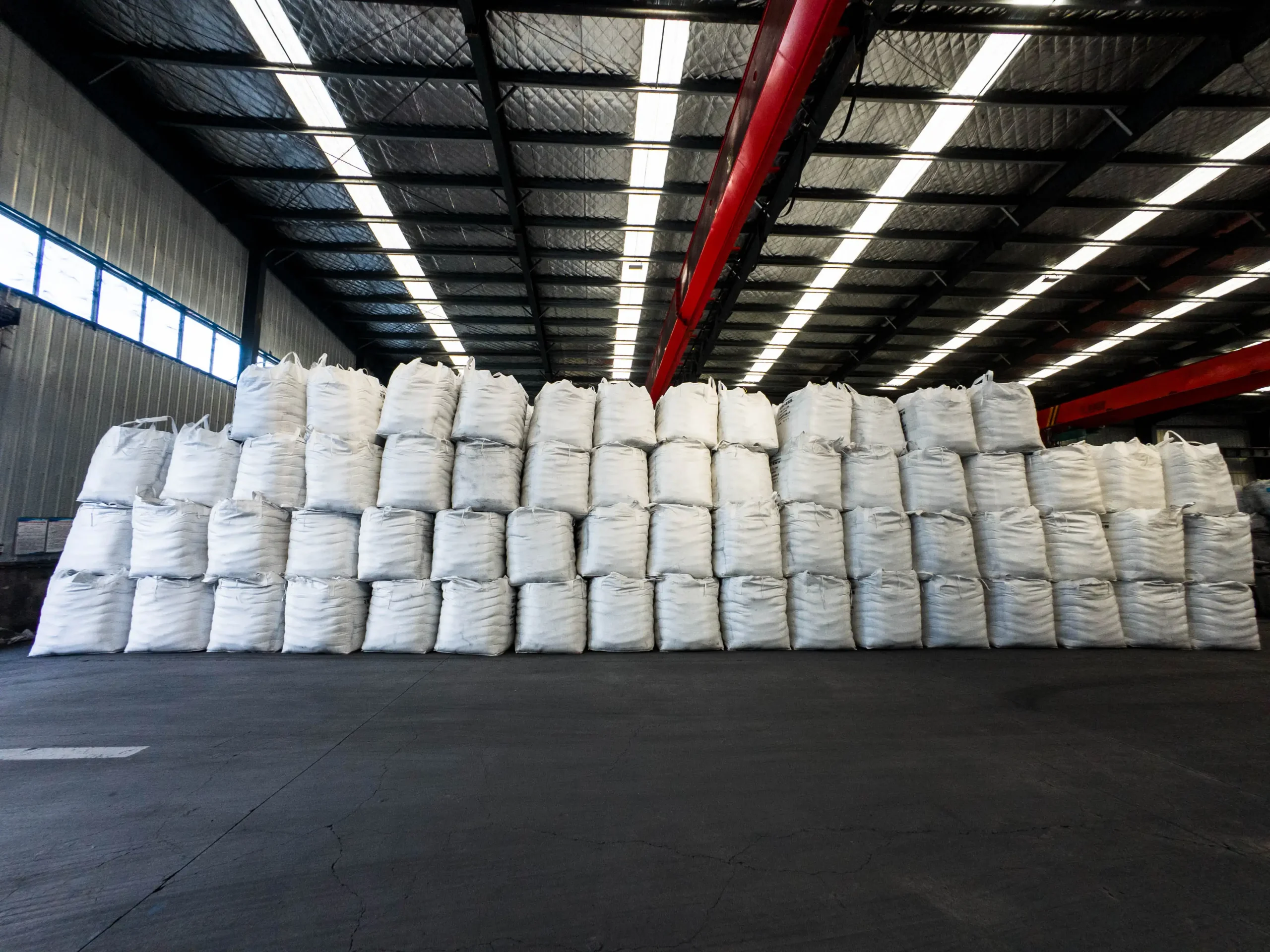
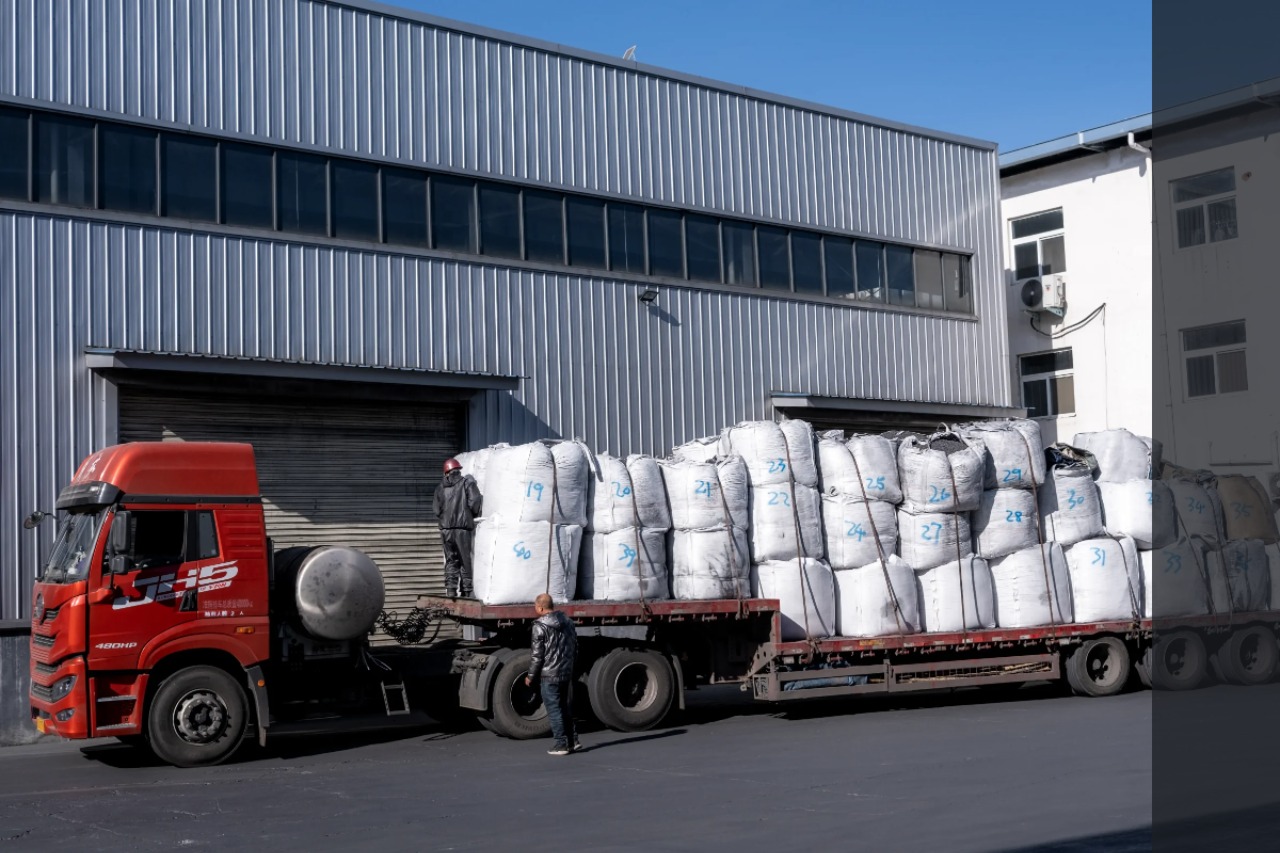
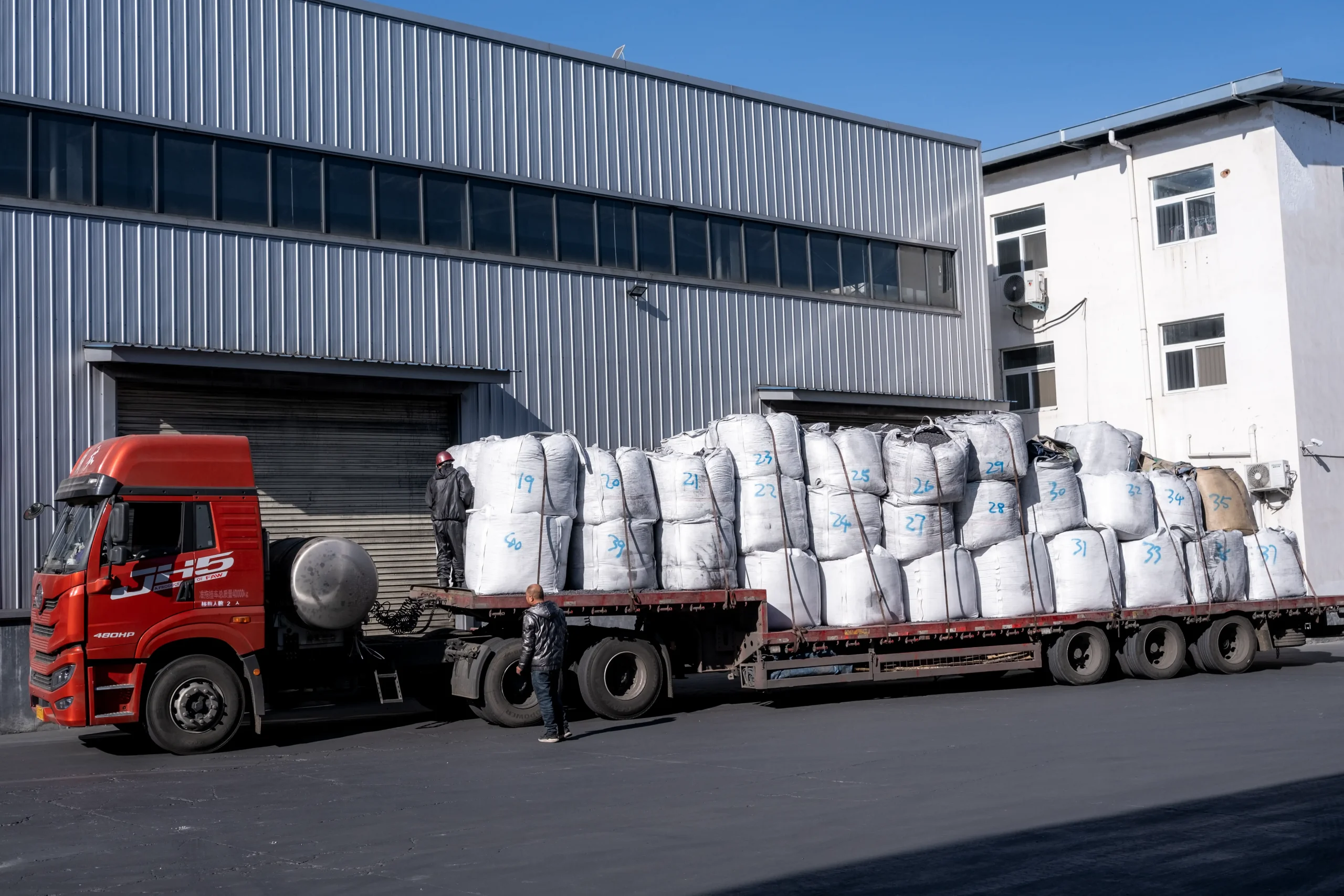
MTGPC
Medium-temperature graphitized petroleum coke, also known as semi-graphitized recarburizer, is the insulation layer of Acheson’s high-temperature graphitized products. The graphitization temperature is in the range of 1700-2700℃. It is a medium-temperature graphitized recarburizer product with high fixed carbon, fast dissolution rate and high absorption rate. It can be widely used in the recarburization of ordinary ductile iron and gray iron with high cost performance.
-
Fixed carbon high
The medium - temperature graphitization temperature is generally between 1500 - 2500 °C, which makes the carbon atoms arrange regularly to a certain extent. The fixed carbon content is generally between 98% - 99%, which can meet the recarburization requirements for the production of most ordinary steels.
-
Low sulfur and low nitrogen
The medium - temperature treatment can also remove sulfur, nitrogen and other impurities to a certain extent. The sulfur content can generally be controlled below 0.5%, and the nitrogen content is around 200 ppm. This can reduce the adverse effects on the properties of steel and ensure the quality of castings.
-
Fast dissolution rate
Compared with high - temperature graphitized recarburizers, the dissolution rate is slightly slower. However, due to its relatively high degree of graphitization, it still has a fast dissolution rate in the molten metal and can replenish carbon elements to the molten metal within a reasonable time.
Catalog Number | Carbon | Ash | Volatile | Sulfur | Size |
---|---|---|---|---|---|
CHYMTGPC-1 | ≥98% | ≥1% | ≥1% | ≥0.3% | 1-5mm |
CHYMTGPC-2 | ≥98% | ≥1% | ≥1% | ≥0.3% | 1-3mm |
CHYMTGPC-3 | ≥98% | ≥1% | ≥1% | ≥0.3% | 0.2-1mm |
CHYMTGPC-4 | ≥97% | ≥2% | ≥1% | ≥0.5% | 0-0.2 |
CHYMTGPC-5 | ≥98% | ≥1% | ≥1% | ≥0.3% | 0.2-2mm |
Physical Properties
1. Appearance
- Medium-temperature graphitized petroleum coke (GPC) typically exhibits a gray-black color with a surface sheen that is slightly lower than that of high-temperature GPC, yet retains a metallic luster
2. Structure
- The material features a dense porous structure, which contributes to its specific surface area and enhances adsorption capacity in chemical processes
- This structure is influenced by the graphitization process, where intermediate phase formation and fiber-like alignment occur at controlled temperatures
3. Hardness and Brittleness
- Medium-temperature GPC demonstrates moderate hardness and brittleness. It maintains its form during transportation but is more prone to fragmentation under significant external forces compared to high-temperature GPC
4. Density
- The density of medium-temperature GPC is moderately balanced, typically ranging between that of regular petroleum coke and high-temperature GPC, ensuring stable mixing in industrial reactions
5. Electrical and Thermal Conductivity
- While it possesses some electrical and thermal conductivity, it is less pronounced than high-temperature GPC. Nonetheless, it is suitable for applications requiring moderate conductivity, such as industrial heating
Chemical Properties
1. Purity
- Medium-temperature GPC has a high carbon content (95%-98%), with most impurities removed during the graphitization process. However, residual impurities may still be present compared to high-temperature GPC
2. Sulfur and Nitrogen Content
- Levels of harmful elements like sulfur and nitrogen are relatively low, meeting stringent requirements for steel production and casting processes. This minimizes adverse effects on steel quality and reduces casting defects
Smelting Performance
1. Absorption Rate
- In metallurgical applications, the absorption rate of medium-temperature GPC is high (85%-90%), enhancing the carbon content in molten iron and reducing smelting time for mid-range/low-end steel products
2. Impact on Casting Performance
- It improves casting properties such as density and reduces gas porosity, though its effectiveness in enhancing comprehensive mechanical properties is slightly lower than high-temperature GPC
3. Steel Scrap Utilization
- Medium-temperature GPC allows for a higher proportion of steel scrap in production, reducing reliance on pig iron. However, stricter quality requirements for steel scrap are needed to ensure final product quality
4. Graphite Core Formation
- It facilitates the formation of graphite cores in cast iron, preventing excessive white cast iron formation and improving processing performance, making it suitable for common cast iron components
1. Raw Material Preparation
Petroleum Coke Selection
- High-quality raw material with **<0.5% sulfur content**, low ash content, and moderate volatile matter is essential for producing MTGPC.
- Why: Low impurities ensure purity and performance in downstream applications.
Crushing & Screening
- The coke is crushed and screened to achieve a 1-3 mm particle size range, optimizing reactivity and graphitization efficiency.
2. Loading the Furnace
Loading Method
- Pre-treated coke is evenly distributed into the medium-temperature graphitization furnace to ensure uniform heat transfer.
Bulk Density Control
- Maintain a loading density of 1.3-1.5 g/cm³ to balance production efficiency and gas emission management.
- Avoid: Excessively high densities may cause uneven heating or gas trapping.
3. Medium Temperature Graphitization Treatment
Power Supply & Heating
- The furnace is heated to 1800°C-2200°C via a controlled power curve, ensuring complete graphitization of the petroleum coke.
Soaking Stage
- The material is held at peak temperature for 12-24 hours, allowing carbon atoms to rearrange into an ordered graphite structure.
- Key factor: Soaking time depends on batch size and product specifications.
Cooling Stage
- Cooling is performed naturally (slow, stress-reducing) or forced (fast, requiring rate control) to prevent cracking.
4. Discharging and Post-Processing
Discharging
- The cooled MTGPC is carefully extracted from the furnace to avoid mechanical damage.
Crushing & Screening
- Depending on market needs, the product is crushed and screened into 0.1-0.8 mm or 0.8-2 mm particle sizes.
Packaging & Storage
- Packaged in sealed containers (e.g., plastic bags with moisture-proof films) to prevent contamination.
- Stored in dry, well-ventilated warehouses, away from humidity and corrosive substances.
1. Dry and Well-Ventilated Storage
- Humidity Control: Maintain relative humidity below **70%** to prevent moisture absorption, which can cause clumping and degrade performance. Inadequate dehumidification during the rainy season (e.g., in southern regions) may lead to moisture ingress from the air
- Ventilation: Ensure air circulation to mitigate moisture retention and prevent localized humidity build-up.
2. Temperature Control
- Recommended Range: Store at 10-30°C (room temperature) to avoid accelerating oxidation reactions.
- Extreme Temperature Precautions:
- Avoid freezing (rare but possible) to prevent structural alterations.
- High temperatures (above 30°C) should be minimized to preserve material integrity
3. Fire Safety Measures
- Prohibition: Smoking and open flames are strictly forbidden due to GPC’s flammability.
- Safety Equipment: Maintain readily accessible fire extinguishers, hoses, and other emergency response tools
4. Pollution Prevention
- Cleanliness: Keep the storage area free from dust, oil, and other impurities to avoid contamination during steelmaking or casting processes
- Handling Protocols: Implement procedures to prevent cross-contamination with reactive materials (e.g., strong oxidizers)
5. Packaging Requirements
- Sealing: Use woven plastic bags or kraft paper bags lined with plastic film to prevent moisture and air ingress, ensuring dryness and stable quality
- Strength: Packaging must withstand handling; large bags (e.g., ton bags) require reinforced handles and seams
- Labeling: Clearly display product name, specifications, weight, production date, and manufacturer information, along with warning labels (e.g., moisture-proof, fire safety)
6. Transportation Methods and Precautions
- Road Transport:
- Ensure cargo areas are clean, dry, and rain-protected; secure goods for long-distance travel to prevent jolting
- Rail Transport:
- Load GPC into containers or covered freight cars; avoid mixing with incompatible materials (e.g., oxidizers)
- Water Transport:
- Use dry, ventilated ship holds; enhance packaging waterproofing to withstand maritime moisture and corrosion risks
- General Precautions:
- Minimize exposure to rain or moisture; address packaging damage or moisture promptly.
- Avoid collisions and friction to prevent particle breakage; maintain smooth driving to reduce dust inhalation risks
Key Technical Considerations
- Temperature Precision: The recommended range (10-30°C) balances energy efficiency and material stability, aligning with industry standards for carbon materials
- Packaging Integrity: Sealing and strength requirements are critical to maintain GPC’s low sulfur and high conductivity properties throughout the supply chain
This structured approach ensures GPC quality and safety from production to end-use, adhering to both operational and environmental standards.