Zhengzhou ChangHeYue New Material CO.,LTd
Graphitized crucible crushing
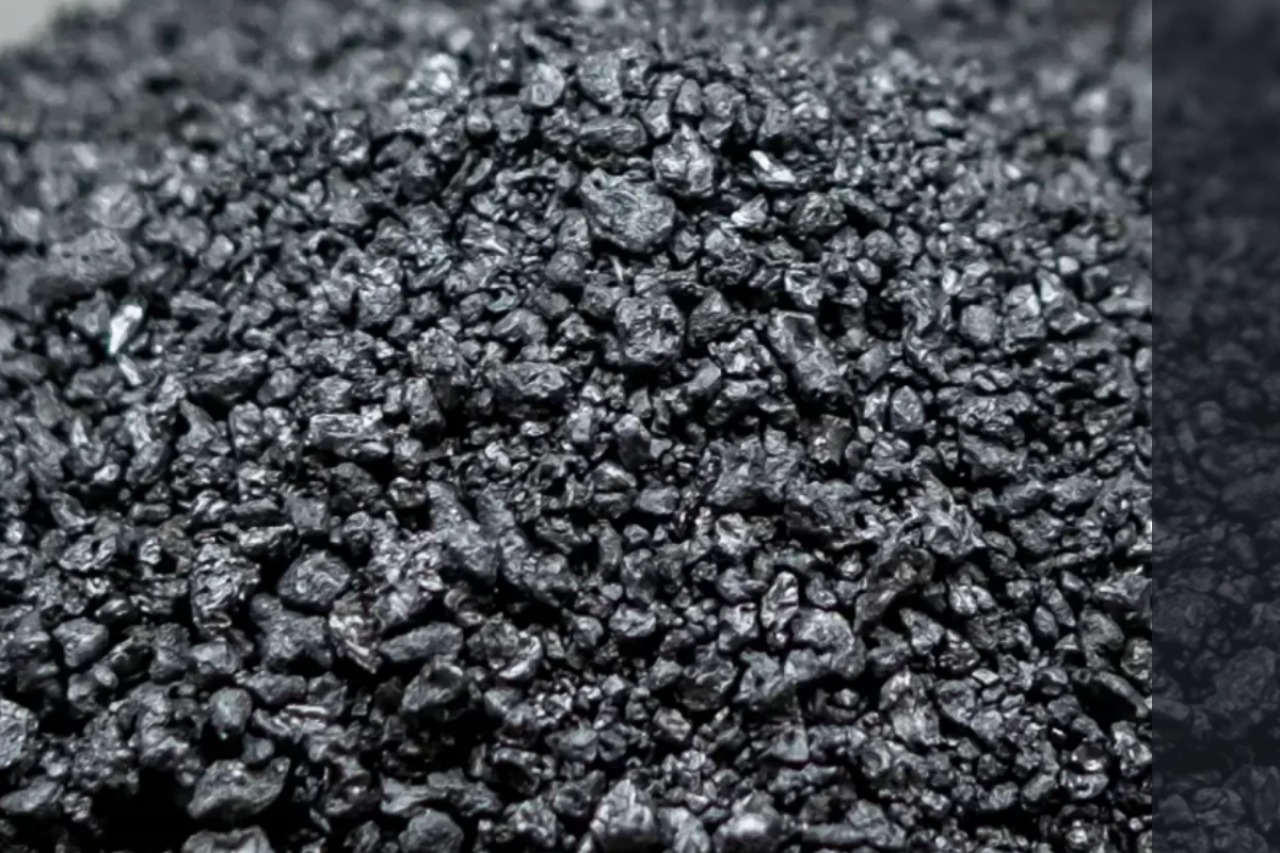
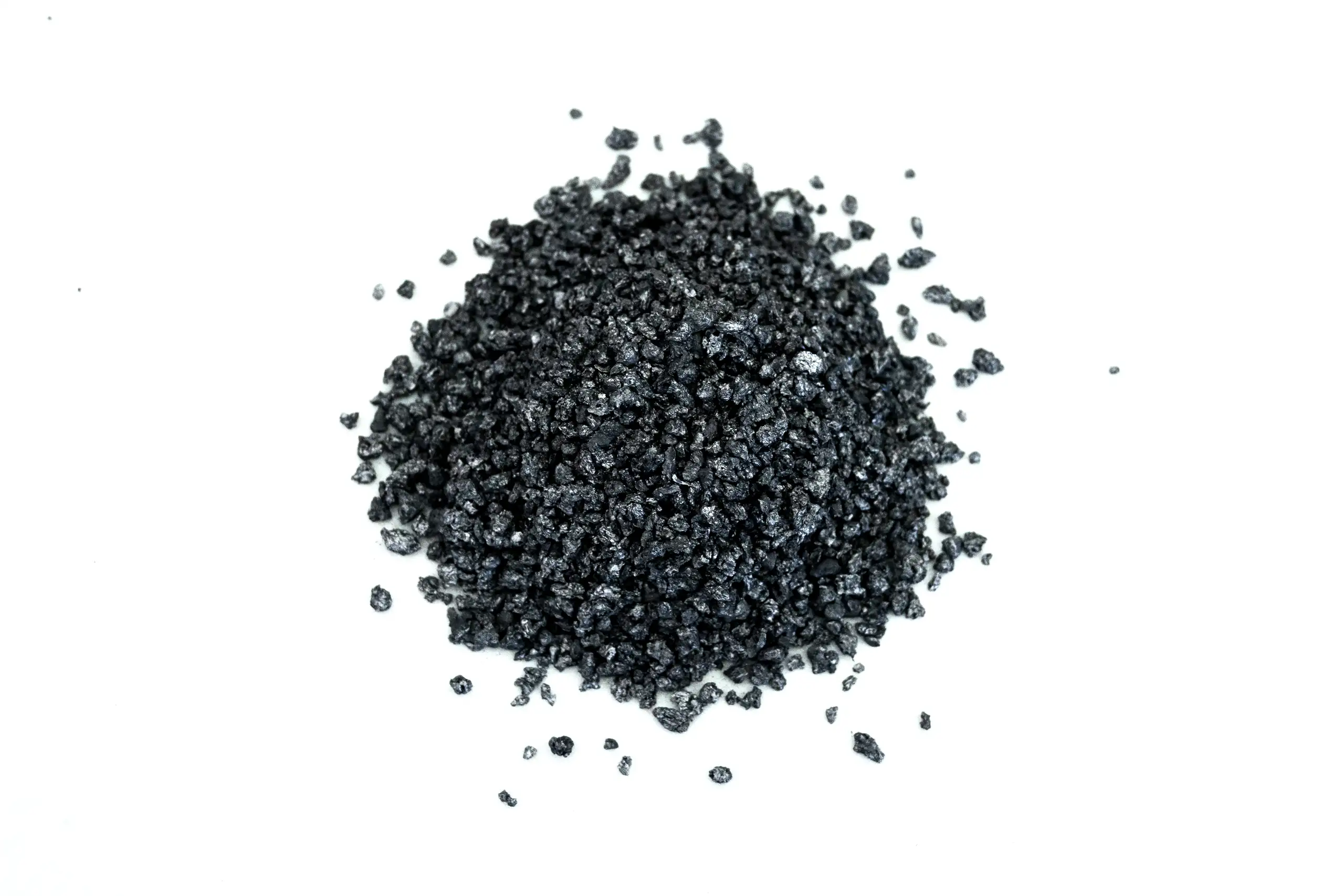
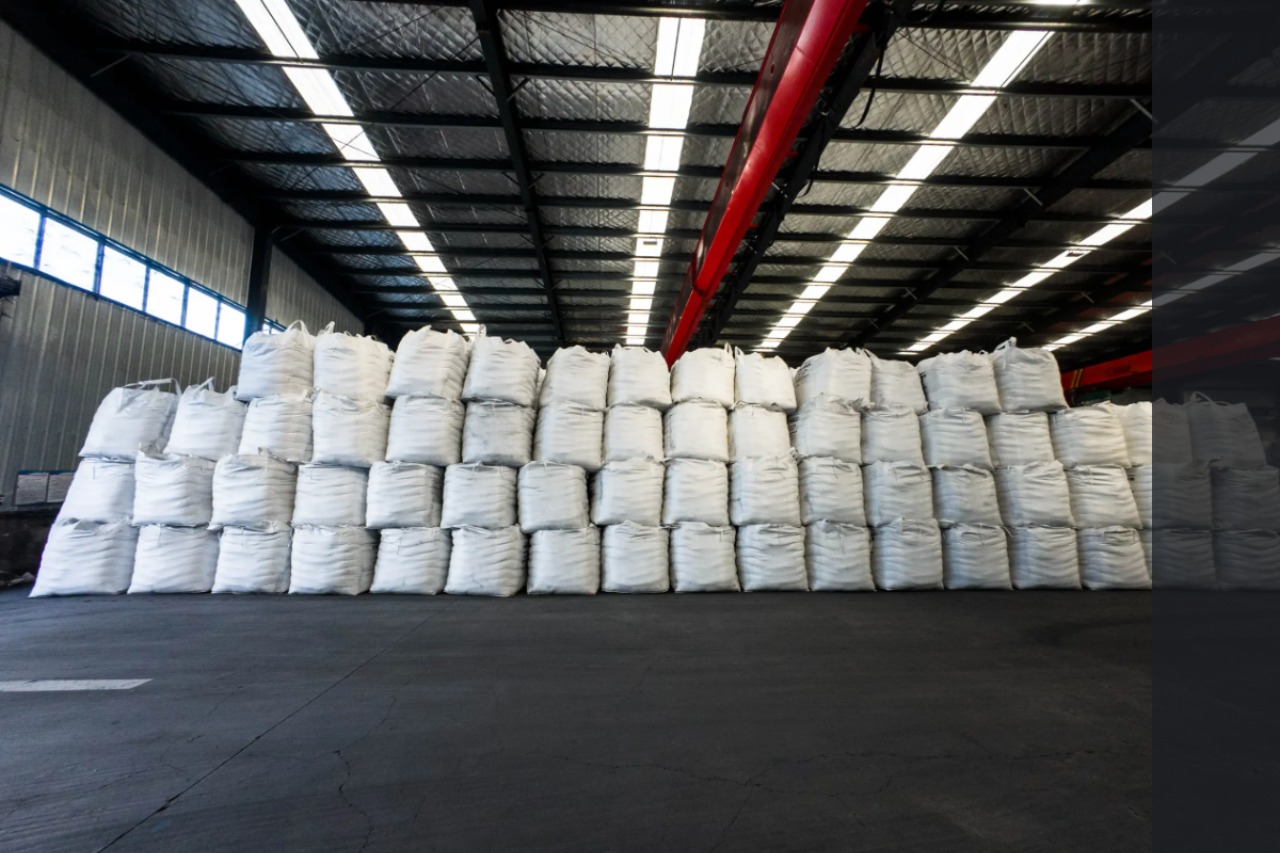
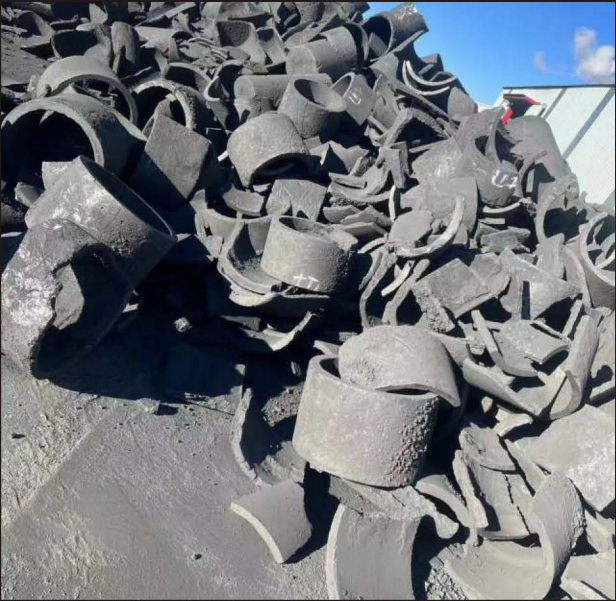
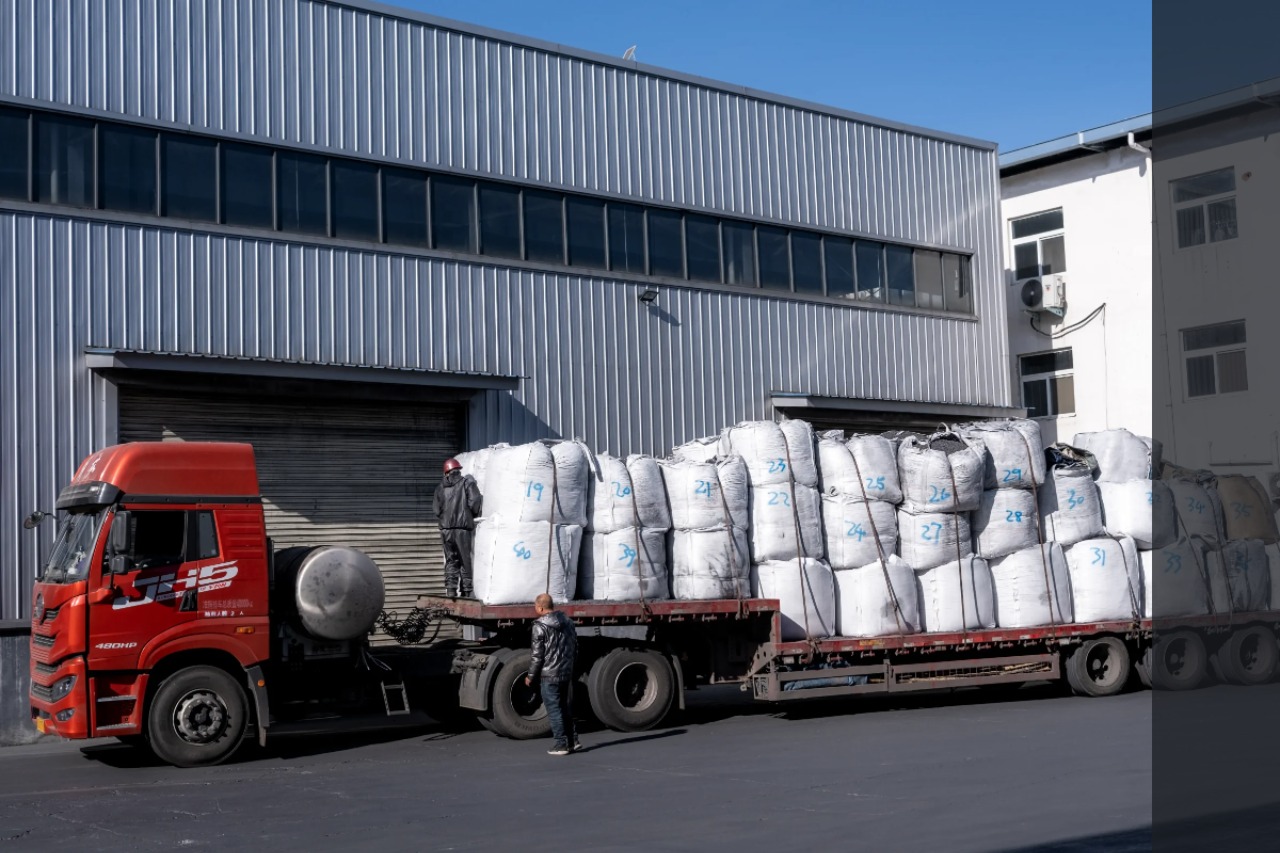
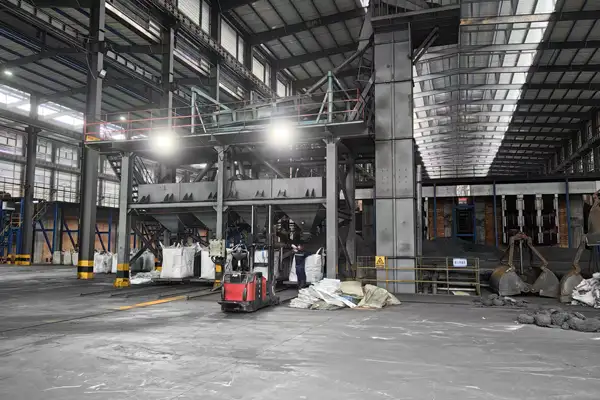
GCC
Graphitized crucible crushing are byproducts produced during the graphitization process of negative electrode materials.
They are cut and crushed from graphitized crucibles.
-
Fixed carbon high
-
Low sulfur and low nitrogen
-
Fast dissolution rate
Catalog Number | Carbon | Ash | Volatile | Sulfur | Size |
---|---|---|---|---|---|
CHYGCC-1 | ≥98.5% | ≥0.8% | ≥0.7% | ≥0.05% | 0-0.2mm |
CHYGCC-2 | ≥98.5% | ≥0.8% | ≥0.7% | ≥0.03% | 0.2-1mm |
CHYGCC-3 | ≥98.5% | ≥0.8% | ≥0.5% | ≥0.03% | 1-5mm |
Product description
Physical Properties
Appearance: Graphitized crucible fragments typically present as irregular chunks that are black or dark gray in color. Their surface exhibits a certain degree of graphite luster, which reflects the underlying graphitized structure.
Density: The density of these fragments is relatively high, usually ranging from 1.8 to 2.2 g/cm³. This high density results from the compact internal structure formed after the graphitization process, allowing them to withstand considerable pressure without easily deforming.
Hardness: Graphitized crucible fragments possess a degree of hardness, yet they also exhibit a certain brittleness. While they may shatter under external impacts, their hardness ensures that, during normal usage—such as grinding and mixing—they will not be easily worn down.
Particle Size Distribution: Being a product of crushed crucibles, the particle size distribution is quite broad, encompassing everything from fine powdery particles to larger blocky fragments. This characteristic influences their applicability in various contexts; for instance, fine particles can serve as additives in paints, while larger particles may be utilized as fillers in applications requiring significant strength.
Chemical Properties
Chemical Stability: Graphitized crucible fragments demonstrate good chemical stability, showing minimal reaction with common acids and bases at room temperature and pressure. This feature allows them to coexist in various chemical industrial environments without contaminating or interfering with the chemical processes they encounter.
Impurity Content: The graphitization process significantly reduces the impurity levels in these fragments, especially concerning detrimental impurities such as sulfur and phosphorus, which are kept at low concentrations. This is crucial when using them as auxiliary materials in metal smelting, as it ensures the purity and quality of the resulting metals.
Oxidation Resistance: Within certain temperature ranges, graphitized crucible fragments possess excellent oxidative resistance. Although graphite can react with oxygen at high temperatures, it has enhanced oxidation resistance compared to ordinary carbon materials, enabling it to maintain structural integrity and performance stability for longer durations—an essential feature for applications in high-temperature environments.
Thermal Properties
High Melting Point: The fragments inherit graphite’s high melting point characteristics, typically around 3000°C. This high melting point allows them to serve as stable container materials in high-temperature melting processes without melting themselves.
Good Thermal Conductivity: They exhibit excellent thermal conductivity, enabling rapid heat transfer to the surrounding environment or contacted substances. In metal melting processes, this thermal conductivity aids in evenly heating the molten metal, thereby improving melting efficiency and product quality.
Low Coefficient of Thermal Expansion: Graphitized crucible fragments have a low coefficient of thermal expansion, which means they experience minimal volume changes during rapid temperature fluctuations. This property helps them maintain structural integrity during the frequent heating and cooling cycles of high-temperature applications, reducing the likelihood of cracking or damage.
1. Raw Material Collection and Screening
- Screening:
- Collect used graphite crucibles and perform a preliminary screen to remove severely damaged, corroded, or highly contaminated samples.
- Select intact crucibles with minimal structural damage to ensure high-quality fragments.
2. Cleaning and Pre-treatment
- Cleaning:
- Use ultrasonic cleaning and chemical methods to remove surface impurities, metallic oxides, and contaminants.
- Rinse thoroughly with clean water and dry completely.
3. Crushing Process
- Coarse Crushing:
- Use jaw crushers to break large crucibles into fragments. Adjust parameters (e.g., feed speed, crushing force) based on equipment capabilities and material characteristics.
- Fine Crushing:
- Further reduce particle size with cone crushers or hammer crushers. Integrate real-time screening to separate fragments by size and continue processing undersized material.
4. Classification and Reprocessing
- Classification:
- Use vibrating screens or air classifiers to categorize fragments into grades:
- Fine Powder: <0.1 mm
- Medium Particles: 0.1–1 mm
- Coarse Particles: >1 mm
- Use vibrating screens or air classifiers to categorize fragments into grades:
- Reprocessing (Optional):
- Fine Powder: Subject to high-temperature graphitization to enhance purity.
- Medium/Coarse Particles: Apply heat treatment or additives to improve hardness and performance.
5. Quality Control and Packaging
- Quality Checks:
- Verify particle size distribution, chemical purity (impurity levels), and physical properties (density, hardness).
- Only approved fragments proceed to packaging.
- Packaging:
- Use sealed packaging (e.g., plastic woven bags with liners) to prevent moisture and contamination.
- Tailor packaging to customer requirements and product grades.
Key Advantages
- Resource Recovery: Maximizes the reuse of scrap crucibles through precise processing.
- Customization: Enables production of tailored particle sizes and grades for diverse applications.
- Quality Assurance: Rigorous checks ensure consistent product performance.
1. Warehouse Environment Requirements
1.1 Humidity Control
- Maintain relative humidity **≤60%** to prevent moisture absorption, which could compromise electrical conductivity and chemical stability.
- Why: Excess moisture may degrade the material’s structural integrity.
1.2 Light Exposure
- Avoid direct sunlight or prolonged UV exposure to prevent structural damage or performance deterioration.
2. Stacking Method
2.1 Segregation by Granularity and Quality
- Store fragments of different particle sizes (e.g., fine powder, medium, coarse) and quality grades in separate zones.
- Key purpose: Prevent cross-contamination and ensure product purity.
2.2 Height Limitation
- Maximum stacking height: 2–3 meters to avoid compressive stress on lower layers.
- Best practice: Use pallets/shelves for stable support and easy access.
3. Transportation Guidelines
3.1 Transport Tool Selection
Distance | Recommended Tools | Key Requirements |
---|---|---|
Short-term | Box trucks or vans | Waterproofing and dust-proofing of cargo areas |
Long-distance | Railway containers or ship containers | Airtight sealing to prevent moisture intrusion |
3.2 Transport Protection Measures
- Handling:
- Handle with care to avoid collisions, drops, or friction that could damage fragile fragments.
- Packaging:
- For fine powder products: Add an extra protective layer (e.g., polyethylene film) to main packaging.
- Monitoring:
- Conduct regular inspections during transit to ensure packaging integrity and address issues immediately.