Zhengzhou ChangHeYue New Material CO.,LTd
High temperature graphitized petroleum coke
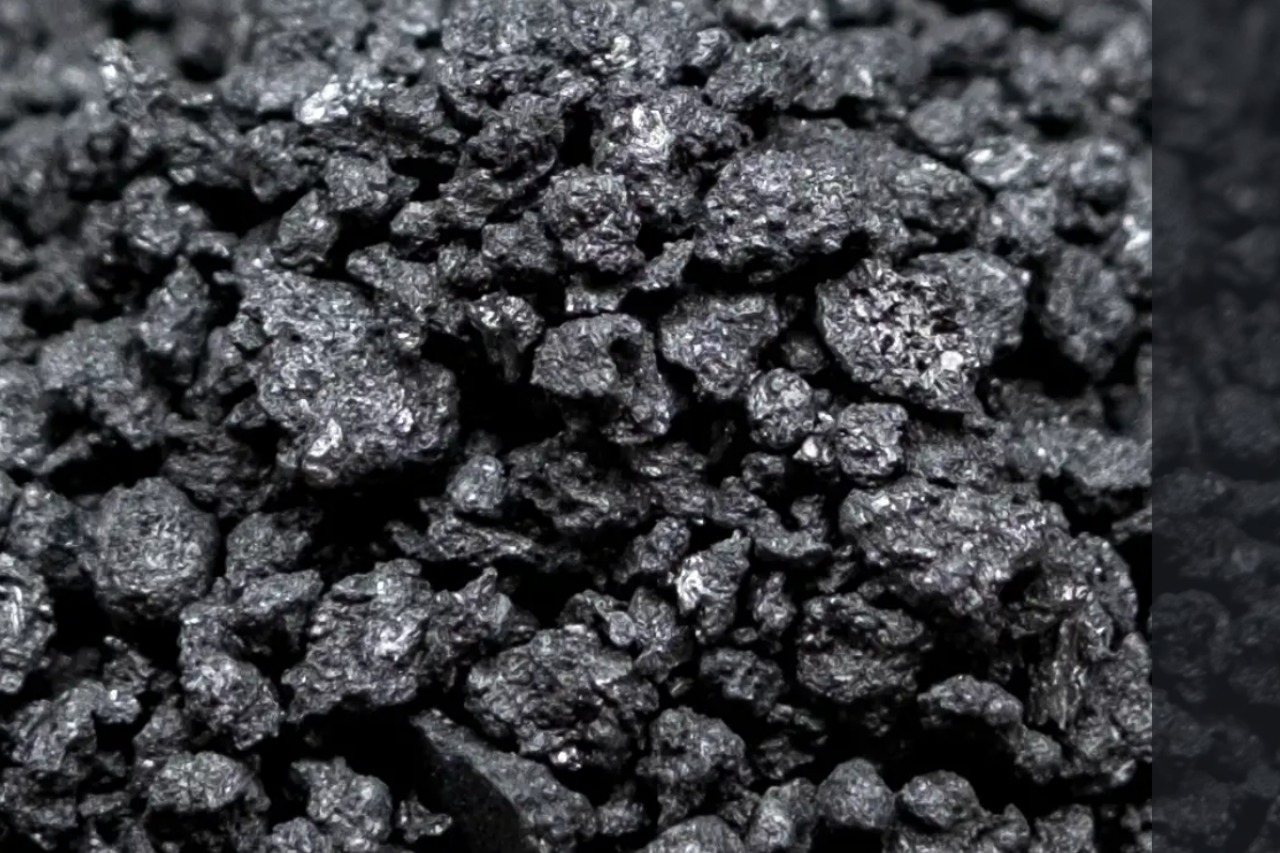
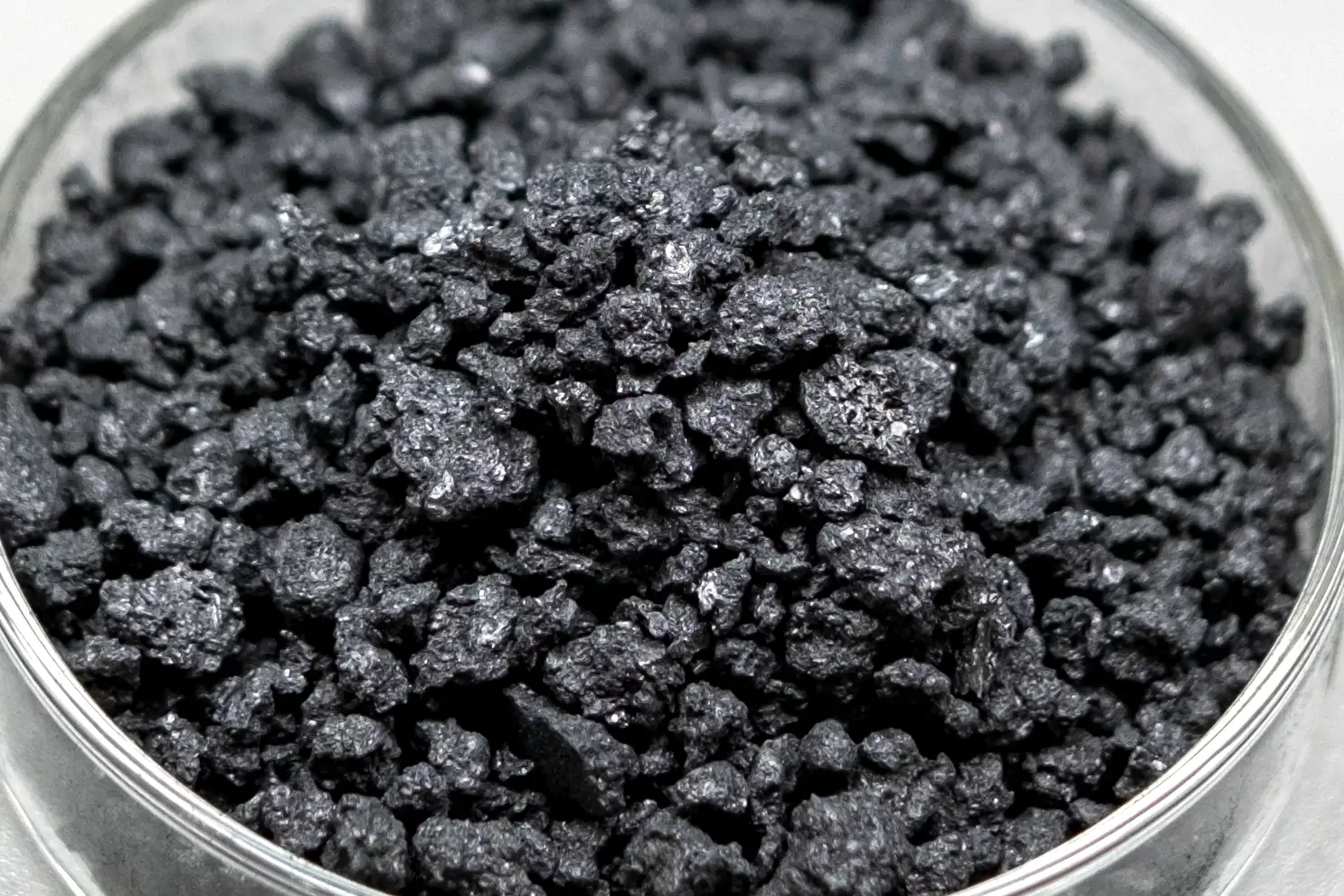
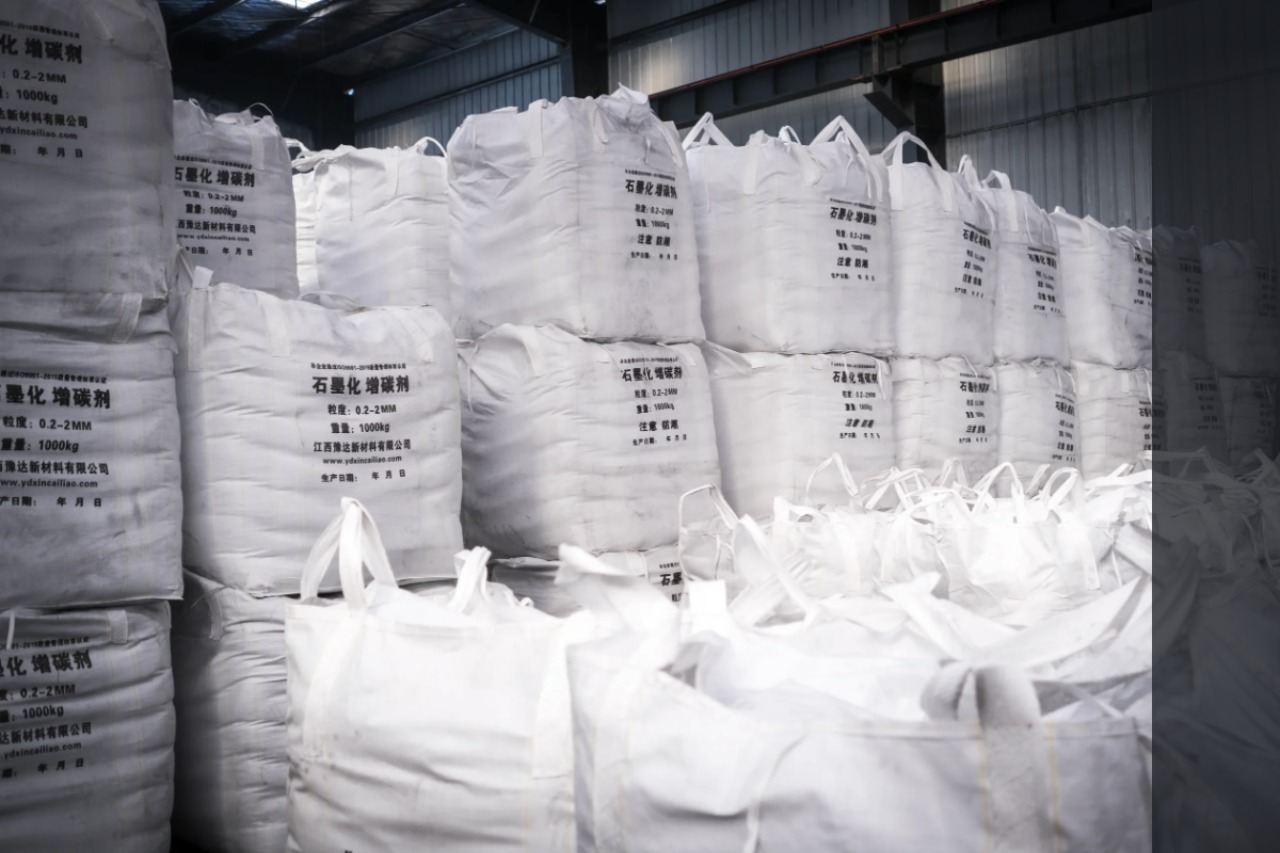
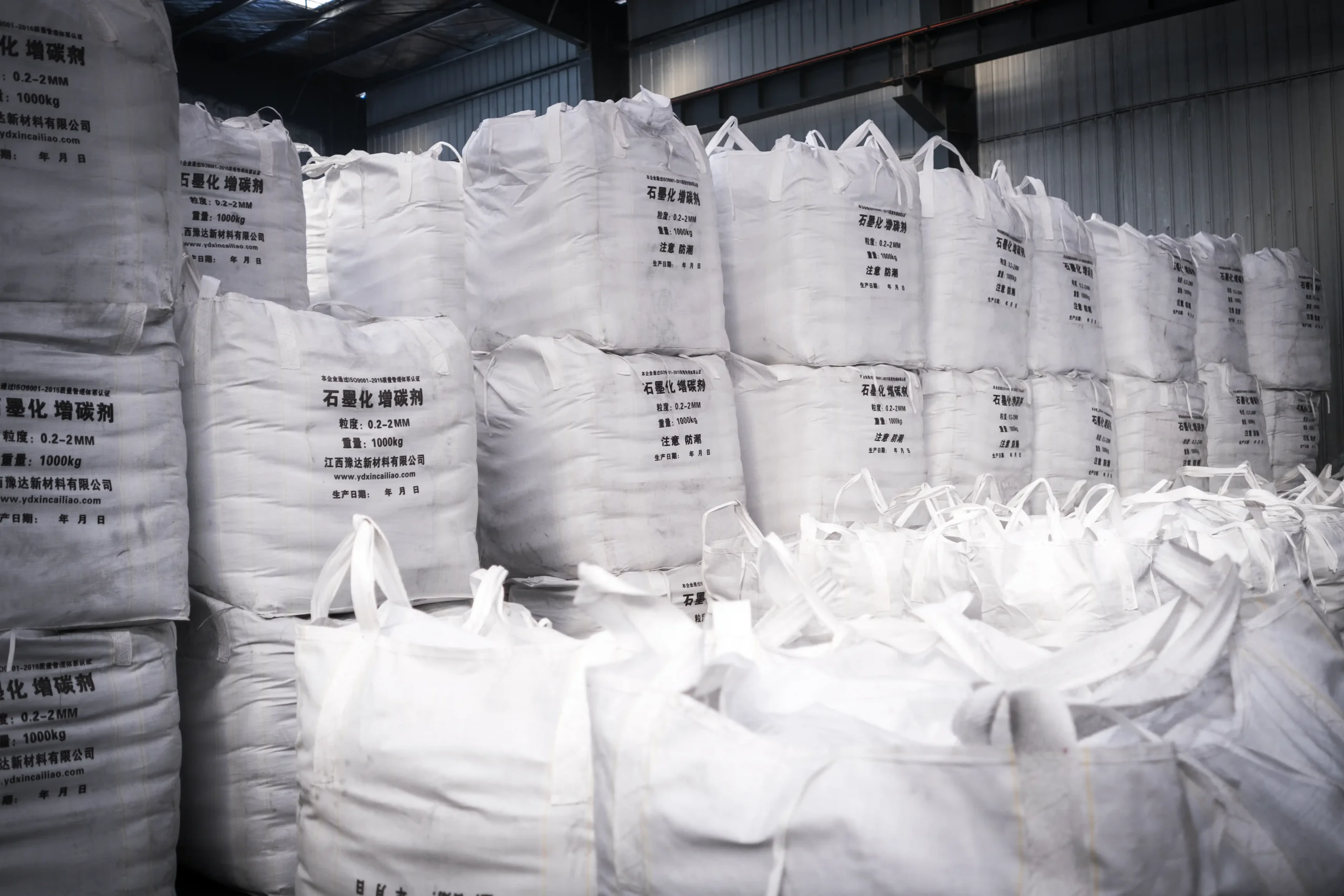
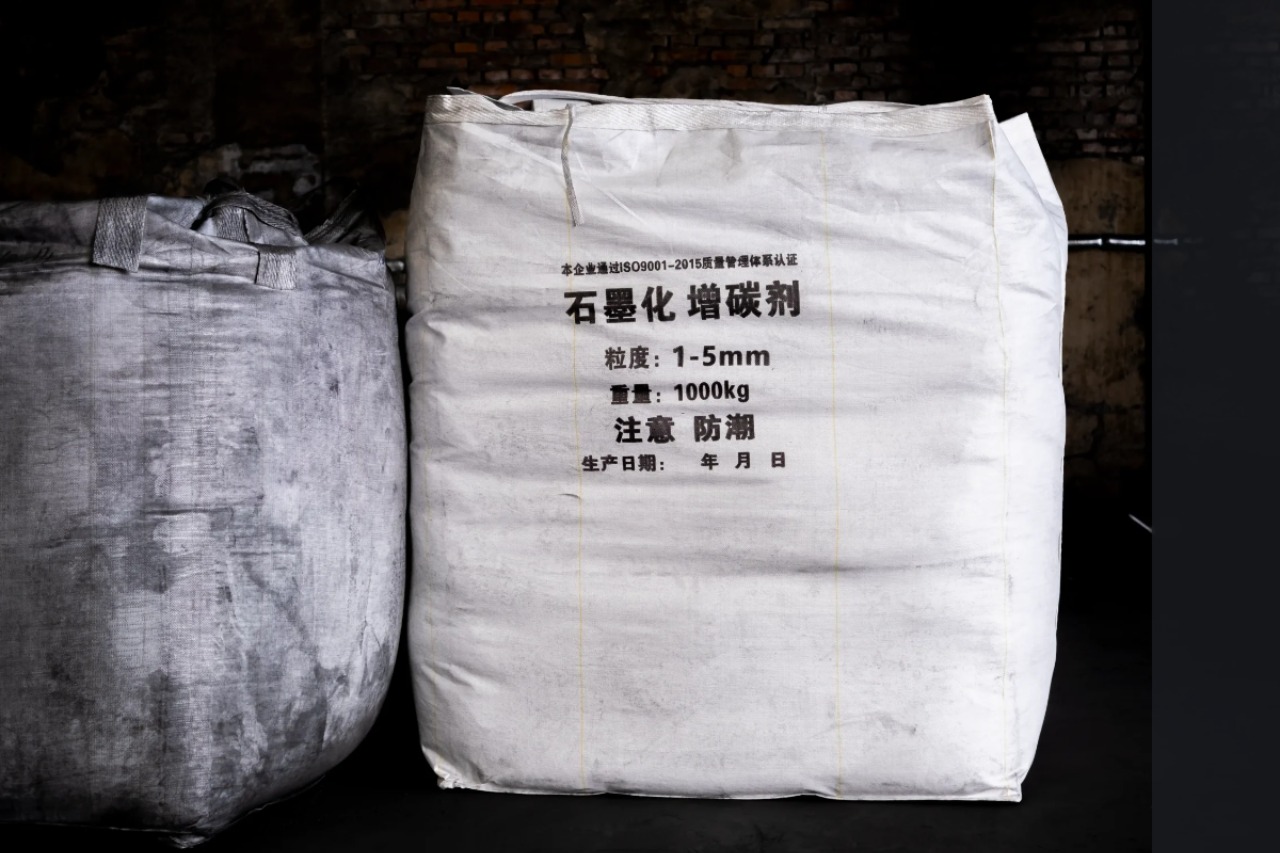
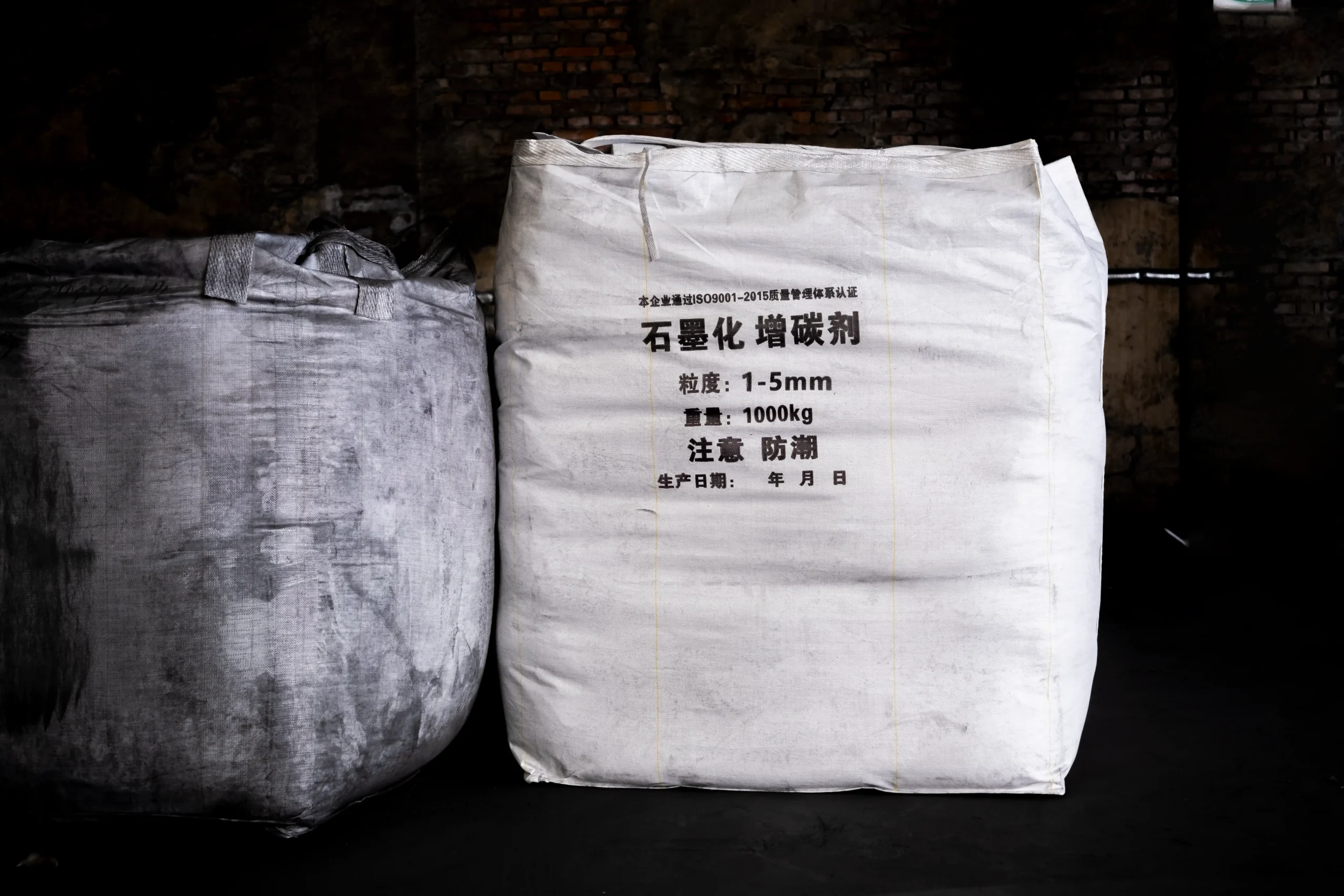
HTGPC
High temperature graphitized petroleum coke is also called full graphitized carburizer. It is the product of the graphitization center of the Acheson furnace. The graphitization temperature is above 3000℃. The product features: high fixed carbon, low sulfur and low nitrogen, fast dissolution speed, high absorption rate. It is the first choice for special steel, high-end castings, ductile iron, and carburizer.
-
Fixed carbon high
Calcined at temperatures above 3000 °C, the degree of graphitization is extremely high. The arrangement of carbon atoms is close to the ideal graphite crystal structure. The fixed carbon content can usually reach 98% or even higher, providing an efficient carbon source for steel and iron smelting.
-
Low sulfur and low nitrogen
Under high - temperature conditions, impurity elements such as sulfur and nitrogen volatilize and are removed in large quantities in gaseous form. The sulfur content can be as low as below 0.02%, and the nitrogen content is usually below 100 ppm. This effectively avoids defects such as gas pores and cracks in castings caused by excessive sulfur and nitrogen content, improving the quality of steel products.
-
Fast dissolution rate
The highly graphitized structure enhances the activity of carbon atoms. They can quickly come into contact with and dissolve in the molten iron or molten steel. At the same time, its porous structure also increases the contact area with the molten metal, further accelerating the dissolution rate. It can uniformly blend into the molten metal in a relatively short time.
High Temperature Graphitized Petroleum Coke
Catalog NO. | Carbon | Ash | Volatile | Sulfur | Size |
---|---|---|---|---|---|
CHYHGPC-1 | ≥98.5% | ≥0.8% | ≥0.7% | ≥0.05% | 1-5mm |
CHYHGPC-2 | ≥98.5% | ≥0.8% | ≥0.7% | ≥0.1% | 1-5mm |
CHYHGPC-3 | ≥98.5% | ≥0.8% | ≥0.7% | ≥0.1% | 0.2-1mm |
CHYHGPC-4 | ≥98.5% | ≥0.8% | ≥0.7% | ≥0.1% | 0-1mm |
Core Physical Properties
- Appearance & Structure Gray-black to black with metallic luster and glossy finish; porous structure design with enhanced specific surface area for improved reactivity.
- Mechanical Characteristics Balanced hardness and brittleness for resistance to deformation during handling/transportation; low density ensures rapid dispersion in molten metal.
- Conductivity Excellent electrical/thermal conductivity for optimized energy transfer during smelting.
Chemical Purity & Stability
- Ultra-High Carbon Content ≥98.5% carbon content (minimized impurities via high-temperature graphitization process); sulfur/nitrogen levels <0.05%.
- Environmental Compliance Low-pollution formulation reduces casting emissions and slag formation, aligning with EU environmental standards.
Metallurgical Performance Advantages
- High Absorption Rate 90%-95% carbon absorption in molten iron, reducing smelting time and energy costs; complete dissolution without residual slag.
- Quality Enhancement Reduces shrinkage/porosity in castings, improving hardness/toughness by 15%-20%; suppresses white iron formation in complex structures.
- Scrap Steel Utilization Enables 30%-50% scrap steel addition, lowering pig iron dependency and production costs.
The production process for high-temperature graphitized petroleum coke is optimized through a systematic approach, ensuring quality and efficiency at each stage. Below is a structured overview with visual enhancements:
1. Raw Material Preparation
- Petroleum Coke Selection
- High-quality petroleum coke with **≤0.5% sulfur content**, minimal ash, and moderate volatility is selected to ensure product purity
- The sulfur content threshold is critical for preventing impurities during graphitization and aligns with industry standards for low-ash feedstock
- Crushing & Screening
- The selected coke is crushed and screened to achieve a 0.5-5 mm particle size range, enhancing reactivity and graphitization efficiency
2. Charging the Furnace
- Furnace Charging Method
- Pre-treated coke is loaded into the graphitization furnace, ensuring even material distribution for consistent heat transfer and graphitization
- Density Control
- The furnace density is maintained at 1.4-1.6 g/cm³ to balance production efficiency and gas discharge, avoiding uneven heat transfer
3. Graphitization Treatment
- Power Supply & Heating
- The furnace is heated to 2800-3000°C using a controlled power delivery curve, fully crystallizing the amorphous carbon structure into graphite
- Soaking Phase
- The material is held at peak temperature for 24-48 hours to allow carbon atoms to rearrange into a denser graphite lattice
- Cooling Phase
- Post-graphitization, the coke is cooled either naturally (to reduce internal stress) or forced (for faster cooling), with careful monitoring to prevent cracking
4. Discharging & Post-Processing
- Discharging
- The cooled coke is carefully extracted from the furnace to avoid mechanical damage
- Crushing & Screening
- The product is resized into 0.2-1 mm, 1-5 mm, 5-8 mm particle ranges to meet market demands
- Packaging & Storage
- Screened coke is sealed in containers and stored in dry, well-ventilated warehouses to prevent moisture and contamination
Key Technical Considerations
- Temperature Precision: The high-temperature range (2800-3000°C) is critical for achieving complete graphitization, surpassing traditional methods (2200-2600°C)
- Density Management: Optimized furnace density ensures uniform heat distribution, reducing energy consumption and production delays
This structured approach ensures high-quality output while maintaining operational efficiency, aligning with industry standards for advanced carbon materials
1. Dry and Well-Ventilated Storage
- Humidity Control: Maintain relative humidity below **70%** to prevent moisture absorption, which can cause clumping and degrade performance
- Environmental Conditions: Store in dry, well-ventilated warehouses to mitigate risks associated with high humidity, especially in rainy seasons
2. Temperature Control
- Recommended Range: Store at 10-30°C (room temperature) to avoid accelerating oxidation reactions
- Extreme Temperature Precautions:
- Avoid freezing (rare but possible) to prevent structural alterations
- High temperatures (above 30°C) should be minimized to preserve material integrity
3. Fire Safety Measures
- Prohibition: Smoking and open flames are strictly forbidden due to GPC’s flammability
- Safety Equipment: Ensure availability of fire extinguishers, hoses, and other emergency response tools
4. Pollution Prevention
- Cleanliness: Maintain a dust-free environment to prevent contamination by oil, dust, or other impurities
- Handling Protocols: Implement procedures to avoid cross-contamination with reactive materials (e.g., strong oxidizers) during storage
5. Packaging Requirements
- Sealing: Use woven plastic bags or kraft paper bags lined with plastic film to prevent moisture ingress and ensure dryness
- Strength: Packaging must withstand handling; large bags (e.g., ton bags) require reinforced handles and seams
- Labeling: Clearly display product name, specifications, weight, production date, and manufacturer information, along with warning labels (e.g., moisture-proof, fire safety)
6. Transportation Methods and Precautions
- Road Transport:
- Ensure cargo areas are clean, dry, and rain-protected; secure goods for long-distance travel to prevent jolting
- Rail Transport:
- Load GPC into containers or covered freight cars; avoid mixing with incompatible materials (e.g., oxidizers)
- Water Transport:
- Use dry, ventilated ship holds; enhance packaging waterproofing to withstand maritime moisture and corrosion risks
- General Precautions:
- Minimize exposure to rain or moisture during loading; address packaging damage promptly
- Avoid collisions and friction to prevent particle breakage; ensure smooth driving and proper ventilation to reduce dust inhalation risks
Key Technical Considerations
- Temperature Precision: The recommended range (10-30°C) balances energy efficiency and material stability, aligning with industry standards for carbon materials
- Packaging Integrity: Sealing and strength requirements are critical to maintain GPC’s low sulfur and high conductivity properties throughout the supply chain
This structured approach ensures GPC quality and safety from production to end-use, adhering to both operational and environmental standards.