Zhengzhou ChangHeYue New Material CO.,LTd
In industrial production, factories impose strict requirements on the particle size of graphite petroleum coke (a common carburizer). These specifications are closely tied to carburization efficiency, absorption rates, molten iron quality, and operational processes. Below is a detailed analysis supported by practical data.
1. Particle Size Impacts Carburization Reaction Speed and Efficiency
The particle size of graphite petroleum coke directly affects its dissolution rate in molten iron. From a chemical reaction perspective, smaller particles have a larger surface area, enabling faster contact and dissolution in molten iron. For example, in a 110 kg high-frequency induction furnace experiment, graphite petroleum coke with a particle size of 0.15–0.18 mm dissolved rapidly due to its high surface area, significantly improving carburization efficiency and shortening production time.
However, in larger furnaces like 600 kg induction furnaces, overly fine particles (e.g., 0.15–0.18 mm) face excessive oxidation losses, reducing effectiveness. In contrast, particles sized 1.16–3.12 mm dissolve quickly with minimal oxidation, making them ideal for large-scale furnaces.
2. Optimal Particle Size Enhances Absorption Rates
The absorption rate of graphite petroleum coke correlates strongly with particle size. In medium-frequency electric furnaces, adherence to proper particle size standards achieves absorption rates exceeding 95%.
- Too fine: Particles float on the molten iron surface, increasing oxidation risks and lowering absorption.
- Too coarse: Incomplete dissolution leads to waste.
Moderate-sized particles ensure uniform distribution in molten iron, maximizing reaction efficiency and minimizing losses.
3. Consistent Particle Size Ensures Molten Iron Quality Stability
Uniform particle size in graphite petroleum coke is critical for even carbon distribution. For mechanical parts requiring high material uniformity, improper particle sizes can cause carbon segregation, resulting in inconsistent casting performance.
Additionally, properly sized graphite petroleum coke contains fewer impurities. For instance, overly fine particles may carry dust, contaminating molten iron, while appropriately sized particles naturally filter out impurities during addition.
4. Proper Particle Size Simplifies Operational Processes
Particle size affects material handling and transportation:
- Too fine: Causes dust pollution, health hazards, and inaccurate dosing.
- Too coarse: Risks clogging feed ports and pipelines.
Medium-sized graphite petroleum coke (e.g., 0.5–5 mm) ensures smooth feeding, precise measurement, and stable production workflows, especially in manual or automated systems.
5. Particle Size Standards for Different Production Scenarios
Furnace capacity dictates graphite petroleum coke requirements:
Furnace Type | Recommended Particle Size |
---|---|
<1 t electric furnace | 0.5–2.5 mm |
1–3 t electric furnace | 2.5–5 mm |
3–10 t electric furnace | 5.0–20 mm |
Ladle covering | 0.5–1 mm |
These standards, derived from extensive industrial practice, ensure optimal carburization across production scales.
By optimizing graphite petroleum coke particle size, factories achieve higher efficiency, lower costs, and superior product quality—key factors driving competitiveness in metalcasting and steelmaking industries.
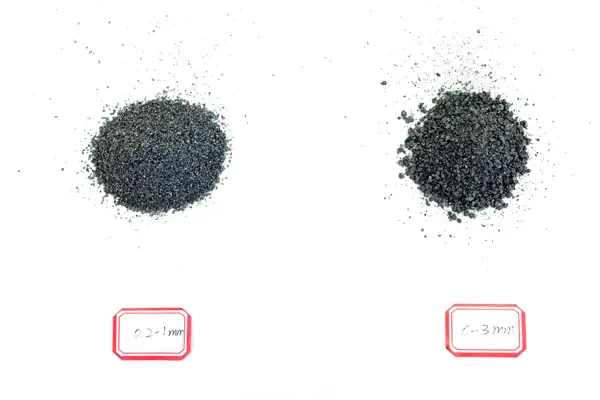